CU Boulder students design adjustable leg prosthetic for growing kids
As parents know very well, the growth spurts of children necessitate new clothes, and for some, that means new prosthetics as well. But the fitting and assembly of a new prosthetic can require significant difficultly and expense on the part of the child and their family.
It can take approximately 15 hours for each new fitting, which requires taking a child out of school and a caretaker to miss a day of work. Also, the cost of a new assembly can be anywhere between $2,500 to $30,000, depending on the sophistication of the device. Perhaps most significantly, an ill-fitting prosthetic can cause long-term damage to the human body.
To help address these issues, a group of mechanical engineering seniors at the University of Colorado Boulder have designed an adjustable lower limb prosthetic called OneLimb Assembly, which will help reduce the number of new fittings and assemblies.
“It’s a simple solution to a really big problem,” Logistics Manager Eileen Reh said.
The team of students from the Paul M. Rady Department of Mechanical Engineering designed and built the prototype for their capstone senior design project.
The OneLimb Assembly, which is composed of a pylon and a foot, features a novel design that allows for an adjustable toe. The tip of the heel plate has a slot and range of pin holes that are measured with each iteration of shoe size. The toe block – a separate piece – is then secured onto the heel plate with a pin that fits into each hole.
The foot can fit a child’s size 13 to an adult’s size 6, while the pylon adjusts continuously from 5 inches to 8 inches. In contrast, the only comparable product currently on the market requires a user to buy a new heel plate every time a child undergoes a growth spurt.
In addition to the costs and the initial day-long appointment that a child and their family must undergo, there are three follow up appointments with a doctor to make sure the assembly is fitting properly.
“They have to repeat this process at least once year, but a child can keep OneLimb for two years, potentially even longer, due to its adjustability,” Reh said.
It’s not just about the time and money that a child and their family will save. With each new fitting and assembly, a child runs the risk of an ill-fitting prosthetic that can lead to health issues in the future.
The added physical stress can cause hip, back and knee pain, and an unbalanced posture and gait can create a wearing of the hips that can eventually cause osteoarthritis.
Reh and the rest of her team want to help mitigate those kinds of health risks.
“What attracted our team to this project is the human factor and the challenge and standard of it,” Reh said. “The continuous drive to work for people and humanity ensures you are doing the best you can as an engineer.”
The team pitched OneLimb Assembly at the New Venture Challenge (NVC), a cross-campus program and competition that gives aspiring entrepreneurs a chance to build a startup through events, programming, community support, mentorship and funding.
The team competed in the female-founder section of the event and came in second place, with a $3,000 cash prize that will help fund their project.
Watch their video pitch here:
[video:video:https://www.youtube.com/watch?v=SkzJzK5ILBI]
“Our next step is to start the patent application process and get our product into the real world,” Reh said. “For our team, the project doesn’t end at Expo or at the end of the semester. There’s still a lot to do.”
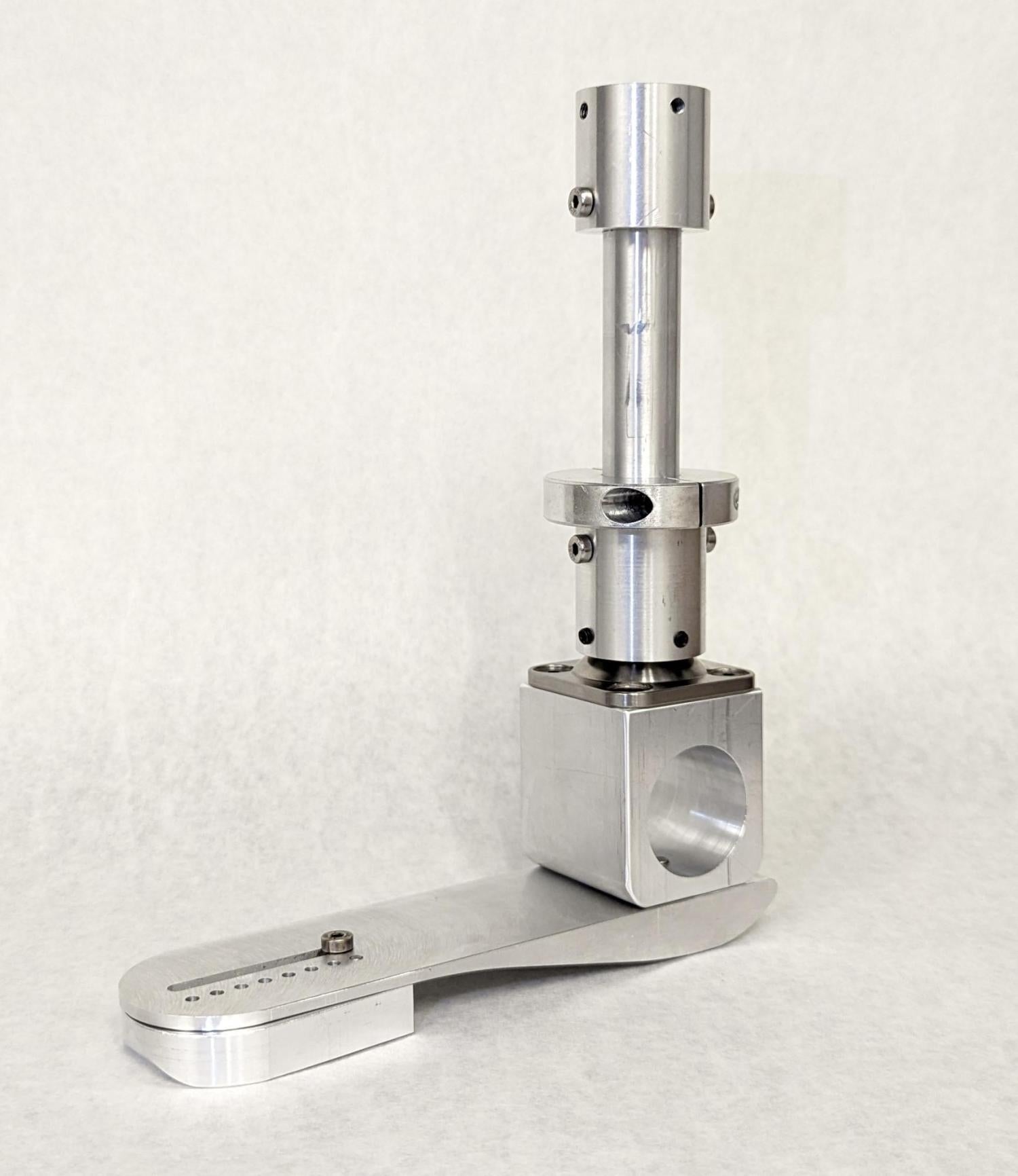