Interning with Electro-Mechanical Products
Spencer White is an undergraduate student in mechanical engineering and a proud member of the CU Cycling Team. He interned with Electro-Mechanical Products during summer 2021.
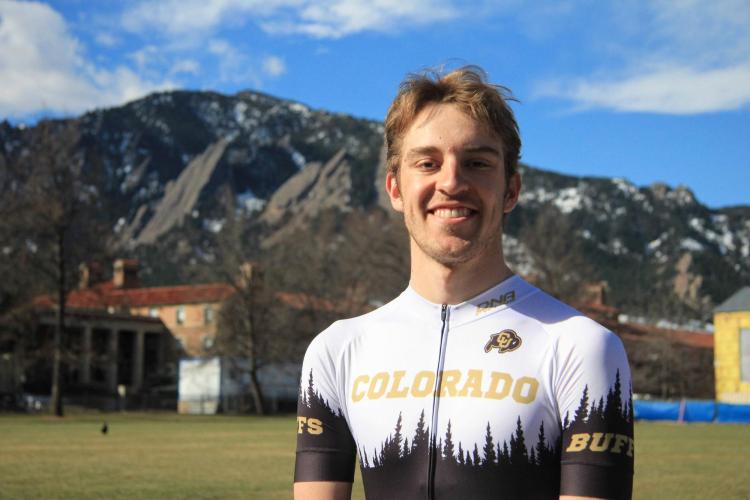
Spencer White
Where did you intern over the summer and what was exciting for you about that opportunity?
This summer I had the amazing opportunity to work as a Manufacturing Engineer Intern at Electro-Mechanical Products Inc. in Lakewood, CO. I first became interested in manufacturing from Prof. Tsai's MCEN 4026 class and wanted to supplement my education with hands-on manufacturing experience. EMP fit the bill perfectly. I was immediately interested in them because of their commitment to creating a high-functioning intern team environment and because we would be working on process improvement projects, something I had not had extensive experience with and was excited to learn more about.
What kinds of projects or tasks were you able to contribute to? What did your day to day work look like?
Our intern team was able to contribute to as many or as few projects as we saw fit over the summer. On day one we were presented with a list of ~20 process improvement projects based on plant need that varied in project complexity. One project I worked on was designing and implementing an automated pneumatic tube-pressing machine to vastly improve downstream manufacturing efficiency. This ~$45000 project utilized machine design skills in I/O based circuits, fluid logic, fixture design, and microcontroller programming.
My day to day work varied between being behind the desk and on the factory floor. Typically I was involved in fixture modeling, creating drawings, talking with machinists, testing and designing circuits and the like. If working in a role like this, be prepared to split your time between desk and floor work!
Was there a particular challenge you encountered that really pushed your engineering skills?
While working on our automation project, we had to interface a fluid logic circuit utilizing solenoids and our programming language. It was an interesting problem designing and testing circuitry to drive a mechanical apparatus with signals originating from a microcontroller, especially in the testing phase. This pushed my engineering and creativity skills to hypothesize all of the numerous possible failure possibilities and design to mitigate these. For example, to uphold project goals of operator safety and reducing scrap, we had to consider if our computer failed, and design for it to fail safely without damaging people or parts.
Did you have any "aha!" moments when you realized that you could use an equation or skill you'd learned in class?
EMP supported the Manufacturing Engineering Interns very well and allowed us relative autonomy in our everyday work, so whatever we were interested in tackling, we did. In my case this involved CAD and creating engineering drawings and working on circuit design. From the ME/EE Circuits course I was able to use transistor math to work with Solid-State Relays (SSR’s) for the first time to take small-power signals and throttle them up to drive high power devices. Having background in op-amps and transistors from the circuits course and in SolidWorks from my CAD class allowed me to contribute to the work in a meaningful way.
What advice would you have for other students interested in working or interning in a related field?
When working or interning in a field related to manufacturing engineering, make sure to keep an open mind and be willing to learn new skills and processes. This field is very dynamic and ever-changing so adaptability is key. Additionally, put effort into team dynamics. You would be surprised at the final results when teams are working at their best and all members of a team are creatively contributing!