Utility Research Lab develops award-winning sustainability tech for 3D printing
Over 460 million metric tons of plastic are created each year and only about 9% is recycled. This has led to ever-growing problems with waste disposal, litter, water contamination, microplastics and a host of other issues.
What if we could rethink our approach to plastics upstream in the manufacturing process before these problems manifest?
Michael Rivera, assistant professor and director of the Utility Research Lab, is doing just that, along with lab members Xin Wen, PhD student, and S. Sandra Bae, PhD candidate.
One of the challenges in recycling is that several types of plastic parts may be used to assemble a single item. These multi-material objects are more difficult, and in some cases near-impossible, to recycle because different plastics need to be processed independently, but cannot be easily separated.
A dissolvable solution
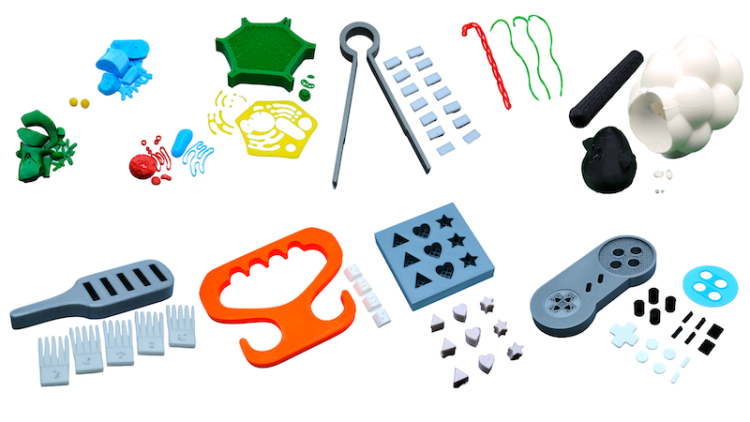
To improve sustainability in 3D printing, Rivera and his team propose using dissolvable interfaces between parts during assembly to simplify their separation for recycling at end-of-life. These interfaces can be made with polyvinyl alcohol (PVA), polyvinyl butyral (PVB), high impact polystyrene (HIPS) or other materials.
Dissolvable materials like PVA are used as support structures, labels and other elements in 3D printed objects. The team goes further by printing PVA in objects themselves to simplify disassembly and recycling. To do so, they developed a computational design algorithm that automates the process of generating and cutting dissolvable interfaces in multi-material 3D-printed objects.
This idea is inspired by the concept of design for disassembly (DfD), “the consideration of ease of disassembly in the design process, aiming to enhance the efficiency of disassembling products by evaluating factors such as time, tools, and effort required for disassembly.”
For their work, the team has been awarded Best Paper (Top 1%) at CHI Conference on Human Factors in Computing Systems in Yokohama, Japan, for Enabling Recycling of Multi-Material 3D Printed Objects through Computational Design and Disassembly by Dissolution.
Sustainable benefits
The team won the Innovation award at CU Boulder’s 2025 Campus Sustainability Summit Student Ideas Showcase
The team has also found that their technique can improve the strength of bonds between different materials in a 3D-printed object. Wen notes, “We ran a bunch of tensile and shear tests that show that varying the parameters of the interface joints can increase the attachment strength” compared to standard multi-material printing.
Alternative manufacturing processes using lego-like building blocks can make reuse and recycling easier, but require more time to build and take apart. The Utility Research Lab’s techniques simplify both of these processes.
Results show their technique can allow for ~90% of the total mass of their designed objects to be recycled. The remaining 10% consists of dissolved material that also has potential for recyclability.
They note in their paper that “recycling 3D printed plastics is a key way to reduce their environmental impacts. Life-cycle assessment has shown recycling 3D printed objects made from PLA and PETG back into printing materials can reduce environmental impacts by more than 50%.”
Wen elaborates, “There are a couple ways you can recycle” these plastics. “There are some DIY recycling machines that you can buy or build off open source designs and there are companies like Printerior that recycle sorted and separated pieces.”
Currently, the team’s technique requires more time to print than conventional multi-material 3D prints due to increased complexity of printing requirements. But they believe with ongoing advancements in printing technology, much of that can be overcome.
For their efforts, the team work won the Innovation award at CU Boulder’s 2025 Campus Sustainability Summit Student Ideas Showcase.
Designs for impact
The team has filed a provisional patent. Rivera explains, “We'd like to be able to license to existing CAD software companies and build an extension inside current 3D printing slicers” by PRUSA and other brands.
They also plan to engage with a local recycling facility this summer to connect the research they are doing in the lab to real-world applications by understanding the logistics and methodologies of plastics recycling at scale.
Looking even further, Rivera sees opportunities in applying this research in the much-larger injection molding industry, a common manufacturing process where molten materials like glass, plastic and metal are injected into a mold to create a form. A pen for example may have separate injection molded parts for the shaft, clip and rubber grip.
Rivera details, “Our algorithm does not really care about the [manufacturing] process per se. If we were to move to injection molding, we would do a multi-stage [process] where you mold the first material, inject the dissolvable on top, and then do another one.”
The team is optimistic for the future of this research.
For those in the maker community, they have developed a plug-in for Grasshopper, a visual programming language in Rhino used for design and fabrication. It is available upon request for non-commercial use.
As for next steps, Rivera says, “For us to have long-term impact, we need the people who run the companies that make the tools. Our conversations with people doing injection molding will be enlightening.”