How glass was made in the ancient Roman world
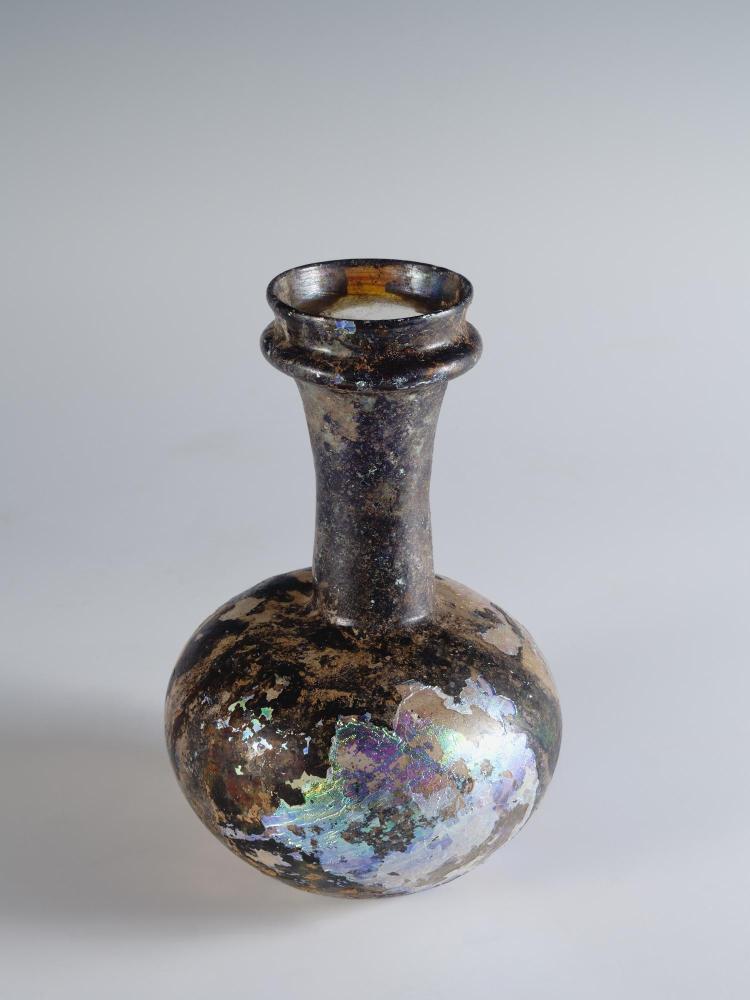
Early on, glassmakers knew how to color glass with the addition of metallic oxides and the colors and fabrics achieved depended upon the qualities and quantities of added materials. Popular for glass were various shades of blue, created by adding cobalt oxide and copper oxide. A small amount of iron caused glass to turn green, while manganese could have created yellowish or purple glass. If a glassmaker desired colorless glass, she or he could add a neutralizing agent (3).
Melted together, the ingredients created molten glass. This substance, too liquid to work with, would be cooled until it hardened into a solid (4). The raw, unshaped glass chunks would be given to glassworkers in separate workshops. The glassworkers would need to remelt the glass in order to make it pliable enough for shaping. A kiln only needed to reach 750 degrees Fahrenheit in order to heat glass enough for it to become workable and that temperature could be accomplished in a simple shielded hearth or average Roman bread oven (5).
Once the glass was plastic enough for working, there were a few methods available for shaping or working glass vessels. Among the earliest methods in Italy produced mosaic glass through a laborious and time-consuming process. Other methods were quicker and more cost-effective, including core-forming, sagging or slumping, free-blowing, and mold-blowing.
Objects in the University of Colorado Museum's collection of Roman glass include representatives of several different kinds of glass manufacture. A 6th to 4th century B.C.E. amphoriskos, for example, was core-formed and a 1st century C.E. pillar-molded bowl was sagged or slumped. A 1st century C.E. flask (pictured at right) was free-blown and a 1st century B.C.E. or 1st century C.E. ribbed cup was mold-blown.
Footnotes
- "It is important to realize that there is a distinct difference between the knowledge of how to make glass and how to work it." Quote from Robert J. Charleston, Masterpieces of Glass: A world history from the Corning Museum of Glass (New York: Harry N. Abrams, Inc. 1980): 12.
- Stuart J. Fleming, Roman Glass: Reflections of Everyday Life (Pennsylvania: University of Pennsylvania Museum, 1997): 10-11.
- Donald B. Harden, Roman Glass from Karanis (Ann Arbor: University of Michigan Press, 1936): 6-9.
- E. Marianne Stern, Roman Mold-Blown Glass (Toledo, Ohio: Toledo Museum of Art, 1995): 42.
- Fleming 1997: 10-11.