Graphene Membranes
Graphene Membrane Electrode
A highly used and facile method for applying graphene to a support membrane is by vacuum filtration, whereby the graphene is mixed well and suspended in a solvent, which is then filtered through the membrane, collecting on top and forming the graphene layer. This works well for inorganic substrates such as alumina anodiscs which won’t dissolve from the solvent, but polymeric membranes have a high chance of dissolving depending on the solvent. Normally, filtering onto alumina anodiscs works well, but for applications where the graphene membrane is required to be flexible such as in a fuel cell, the notoriously brittle anodiscs are a no-go. Here, we build on our previous work by replacing the anodisc membrane with a flexible membrane that is capable of withstanding the choice solvent during filtration. Replacing the rigid and brittle anodisc membrane with a flexible membrane enables this graphene membrane fabrication method to be performed in a continuous roll-to-roll process in the future.
The graphene membrane is made by first exfoliating graphite in NMP via sonication, and then filtering that through a thermal induced phase inversion (TIPS) microporous membrane processing support (MMPS) using a vacuum filtration apparatus. Then, a polymer dope is poured on top and cast with a blade to a certain thickness before being submerged in a coagulation bath to undergo phase inversion. This was done for smaller sized membranes used previously as well as for the current scaled up, larger membranes. Performance properties remained similar between the two sizes.
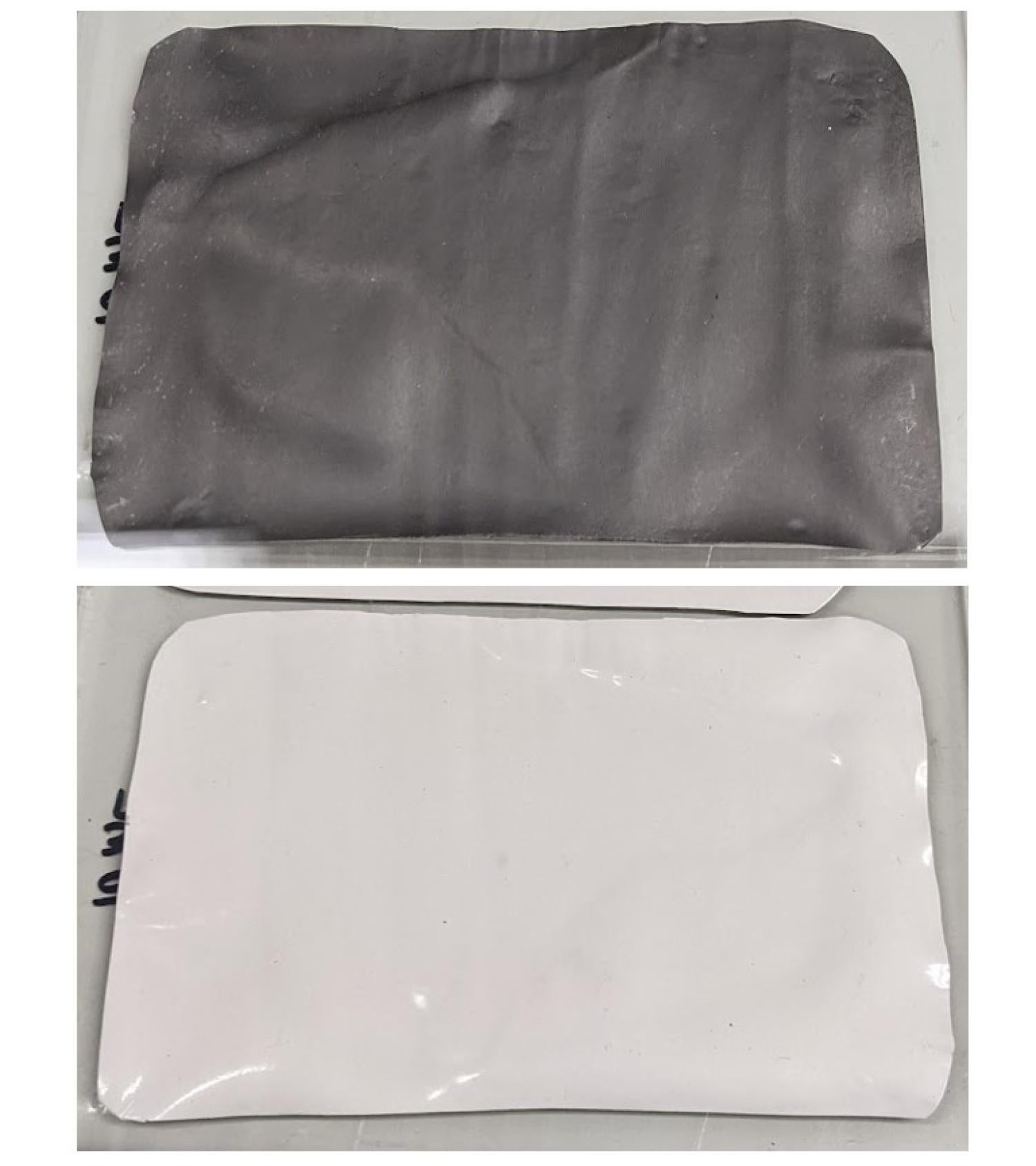
Integrated graphene/PSF membrane showing graphene layer (top) and PSF layer (bottom).
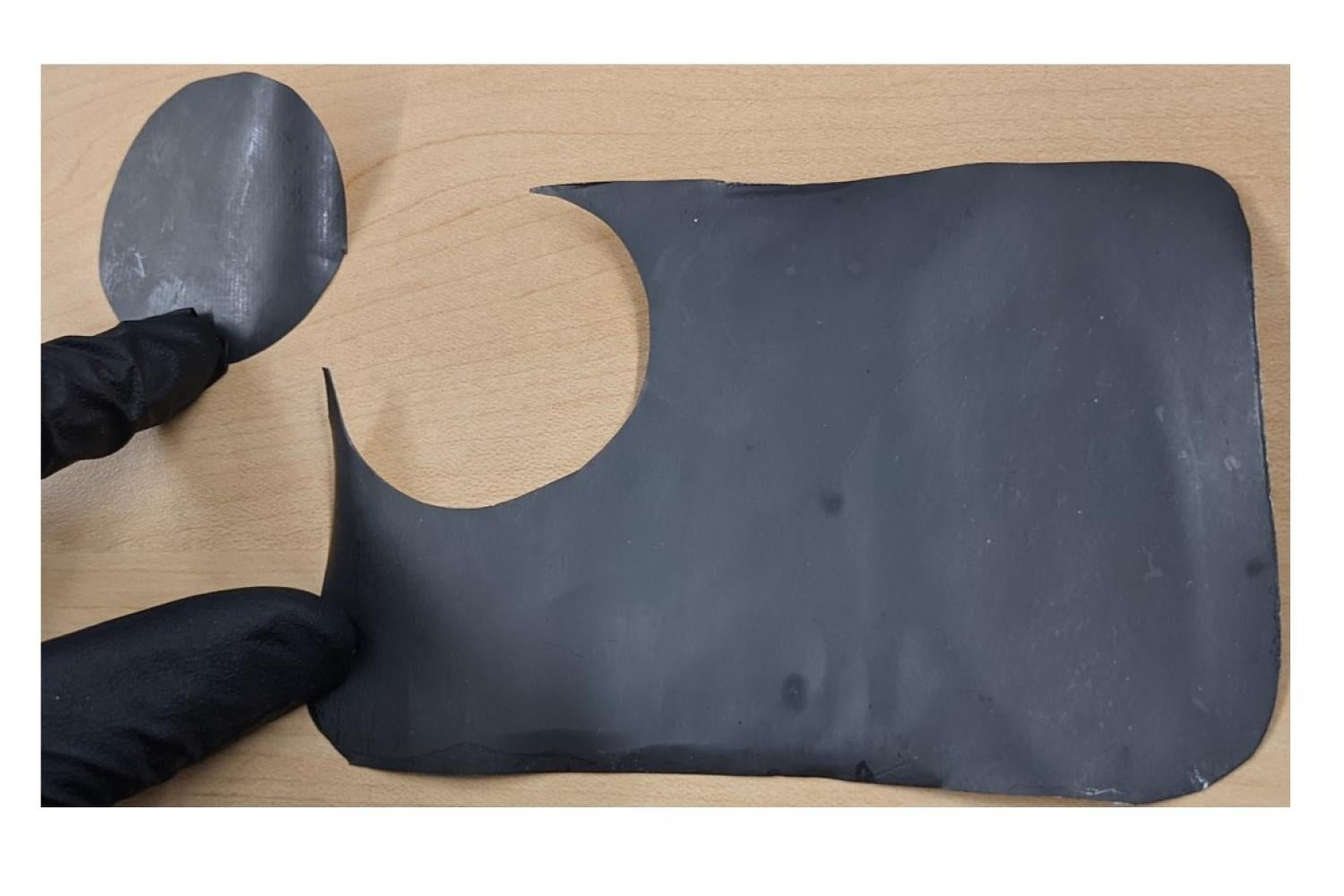
Graphene/PSF membrane samples of both the smaller, testing coupon size and the actual scaled-up, larger size.
Acknowledgements
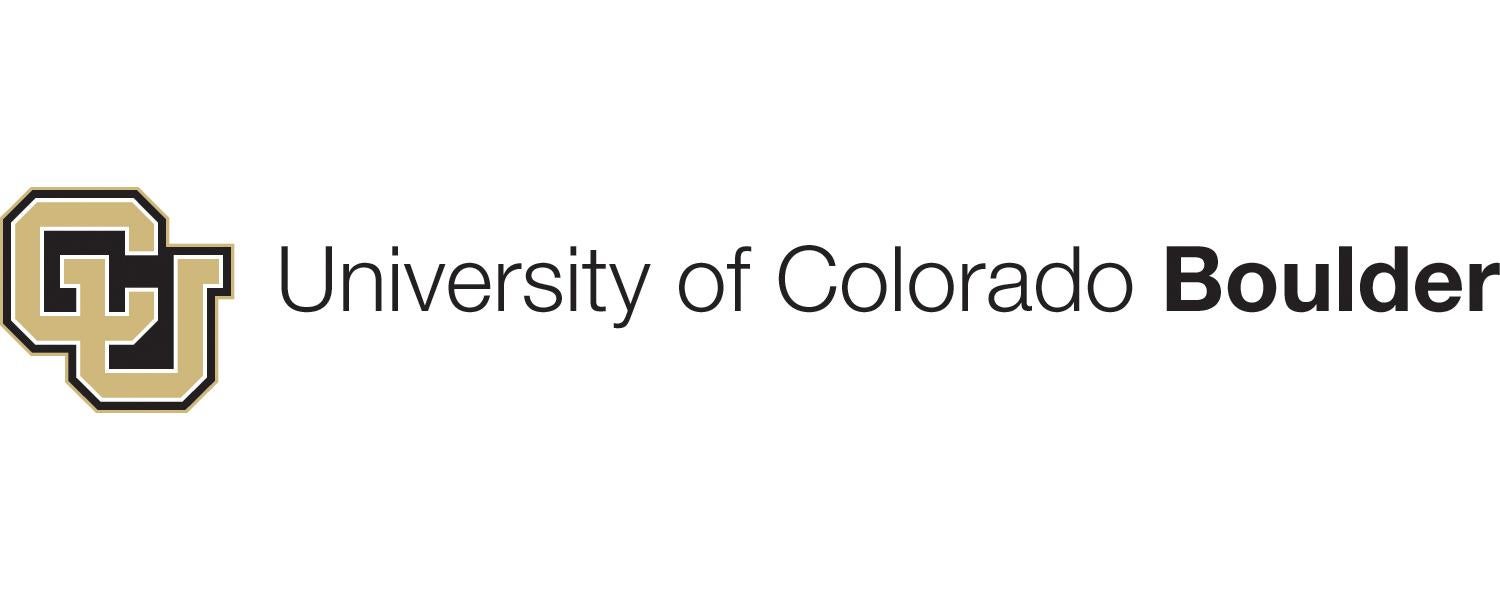