Electric Vehicles
Recent research in this area is directed at substantially reducing the loss of drivetrain power electronics over standard EPA drive cycles. These gains are achieved through a new composite converter approach, with demonstrated reduction in average loss by a factor of 2-4. Earlier research includes power conversion for on-board chargers and for facilitation of a 42 VDC standard.
Composite Converter Architectures: Beyond Multilevel Modular Conversion
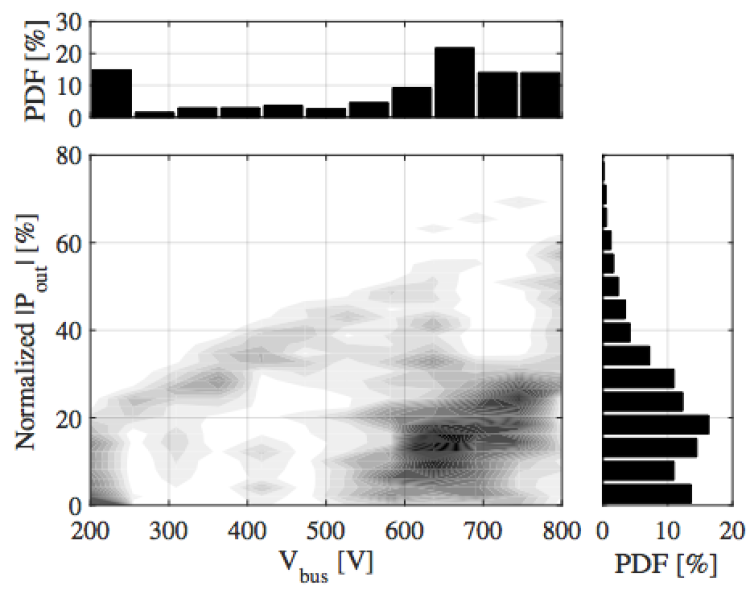
Distribution (PDF) of electric vehicle DC bus voltage and power for a simulated US06 (aggressive) drive cycle.
- H. Chen, K. Sabi, H. Kim, T. Harada, R. Erickson, and D. Maksimovic, "A 98.7% Efficient Composite Converter Architecture with Application-Tailored Efficiency Characteristic," IEEE Energy Conversion Congress and Exposition, Sept. 2014.
- H. Chen, K. Sabi, H. Kim, T. Harada, R. Erickson, and D. Maksimovic, "A 98.7% Efficient Composite Converter Architecture with Application-Tailored Efficiency Characteristic,"IEEE Transactions on Power Electronics, vol. 31, no. 1, pp. 101-110, Jan. 2016.
Conference paper [1] and updated journal paper [2] describe a new composite converter approach and its application to electric vehicle drivetrains. - H. Kim, H. Chen, D. Maksimovic, and R. Erickson, “Design of a High Efficiency 30 kW Boost Composite Converter,” IEEE Energy Conversion Congress and Exposition, Sept. 2015.
This paper documents design and experimental results of a 30 kW boost composite converter for an electric drivetrain application. - H. Chen, H. Kim, R. Erickson, and D. Maksimovic, "Electrified Automotive Powertrain Architecture Using Composite DC-DC Converters," IEEE Transactions on Power Electronics Jan. 2017.
Comparison of efficiency vs. power for conventional boost (solid line) vs. composite (experimental data points), 250 V : 650 V, 30 kW rated converters. It is remarkable that 98% efficiency is maintained down to nearly zero power.
Options for performing the boost function in EV drivetrains are compared using a calibrated loss model, to predict total loss over standard EPA drive cycles, as well as size of the reactive elements. The composite converter approach reduces the loss over typical drive cycles by a factor of approximately four, while also reducing the size of the system film capacitors. - U. Anwar, H. Jin, H. Chen, R. Erickson, D. Maksimovic, and K. Afridi, “High Power Density Drivetrain-Integrated Electric Vehicle Charger,” IEEE Energy Conversion Congress and Exposition, Sept. 2016.
- H. Kim, H. Chen, D. Maksimovic, and R. Erickson, “Composite Converter Design Based on Drive Cycle Weighted Losses in Electric Vehicle Powertrain Applications,” IEEE Energy Conversion Conference and Exposition, Sept. 2016.
- H. Kim, H. Chen, Z. Cole, B. Passmore, K. Olejniczak, R. Erickson, and D. Maksimovic, “SiC Electric Vehicle Composite Boost Converter with 23 kW/L Power Density,” IEEE Applied Power Electronics Conference, Mar 2017.
- H. Kim, H. Chen, J. Zhu, D. Maksimovic, and R. Erickson, “Impact of 1.2kV SiC-MOSFET EV Traction Inverter on Urban Driving,” IEEE Workshop on Wide Bandgap Power Devices and Applications, Nov. 2016.
Earlier Work Related to Vehicle Power Electronics
J. Hong, D. Maksimovic, R.W. Erickson, and I. Khan, “Half-Cycle Control of the Parallel Resonant Converter Operated as a High Power Factor Rectifier”, IEEE Transactions on Power Electronics, vol. 10, no. 1, pp. 1-8, January 1995.
Stephen W. Anderson, Robert W. Erickson, and Ronald A. Martin, “An Improved Automotive Power Distribution System Using Nonlinear Resonant Switch Converters,” IEEE Transactions on Power Electronics, January 1991.
- Stephen W. Anderson, Robert W. Erickson, and Ronald A. Martin, “An Improved Automotive Power Distribution System Using Nonlinear Resonant Switch Converters,” IEEE/SAE Workshop on Automotive Power Electronics, August 1989.
- Robert Erickson, Adan Hernandez, Arthur Witulski, and Renjie Xu, “A Nonlinear Resonant Switch,” IEEE Power Electronics Specialists Conference, 1989 Record, pp. 43-50, June 1989. Also in IEEE Transactions on Power Electronics, vol. 4 no. 2, April 1989, pp. 242-252.