Embedded Magnetic Sensing Method for Soft Actuators
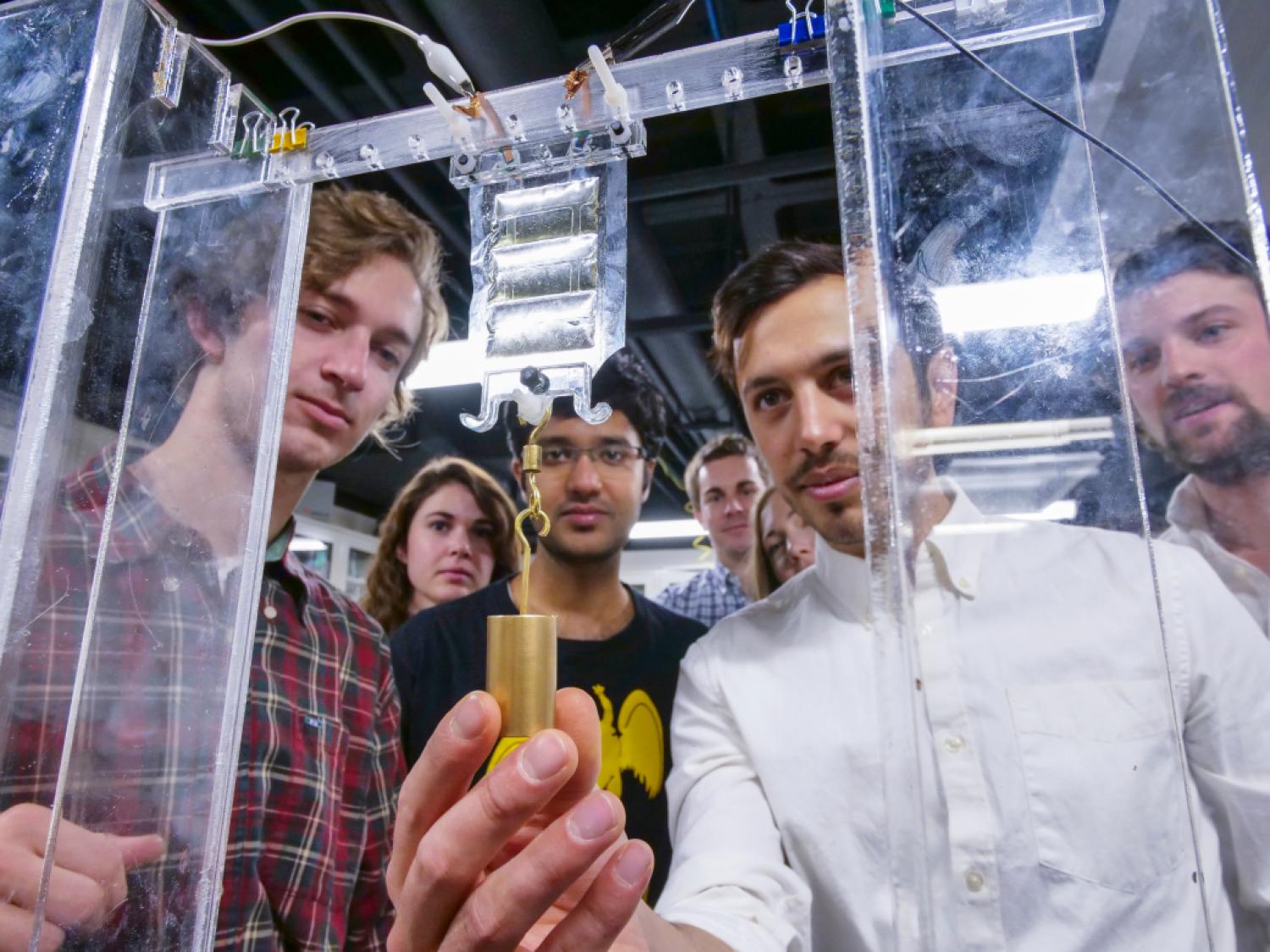
This invention maps changes in magnetic field strength to changes in actuator shape without seeing noise from the actuator or reducing performance.
Background
The field of soft robotics has been rapidly gaining traction due to the deformable and compliant nature of the structural components. These qualities allow for improved adaptability - when compared to the capabilities of conventional, rigid robots - in unstructured environments. In the domain of both traditional and soft robotics, integrating a reliable sensing mechanism with the actuation method is necessary for the robot to interact with its environment. Therefore, having an on-board sensing mechanism is necessary for creating compact, untethered systems.
Technology
To address some of the shortcomings of current sensing methods used for electrohydraulic actuators, such as HASELs, researchers at the University of Colorado explored the idea of using a magnetic sensing approach to measure the change in shape, specifically linear displacement, of a folded HASEL actuator. These actuators are driven by a very low current, which emits a negligible magnetic field. By sandwiching the actuator between an off-the-shelf magnetometer and a magnetic component, as shown in the figure below, they were able to map changes in magnetic field strength to changes in the actuator shape without seeing any noise from the actuator or reduction in performance.
Benefits
- High resolution of 0.1 mm
- Fast sampling rates up to 1 kHz
- Modular design; easy to scale up for larger systems
- Elegant fabrication process
- Clean signal; decoupled from HV noise
Applications
- Soft continuum robots
- Grippers and manipulators
- Terrain detection for mobile robots
- Embedded sensing for orthotics and prosthetics
- Soft robotic platforms with low current usage
Nicole Forsberg: nicole.forsberg@colorado.edu
The Newsroom
For marketing and communication inquiries or news tips, contact Daniel Leonard, senior marketing and communications specialist for Venture Partners at CU Boulder.
For media inquiries, please visit colorado.edu/news/formedia.