Ultra-High Temperature Ceramics
Introduction
The design of hypersonic flight vehicles is characterized by stringent requirements like achieving sharp leading edges to maximize lift-to-drag ratios while experiencing extreme external gas temperatures, which can reach upwards of 10,000K. Designers must contend with the reality that convective heat transfer rates between this hot gas and vehicle surface increase with decreased size of these leading edges, making most common engineering materials such as aluminum or titanium, warp, melt or even vaporize. This reality has motivated fundamental research into a new class of materials known as Ultra-High Temperature Ceramics (UHTC). These materials exhibit a unique combination of refractory and oxidation-resistant properties which allow them to survive the extreme heating environment encountered in hypersonic flight.
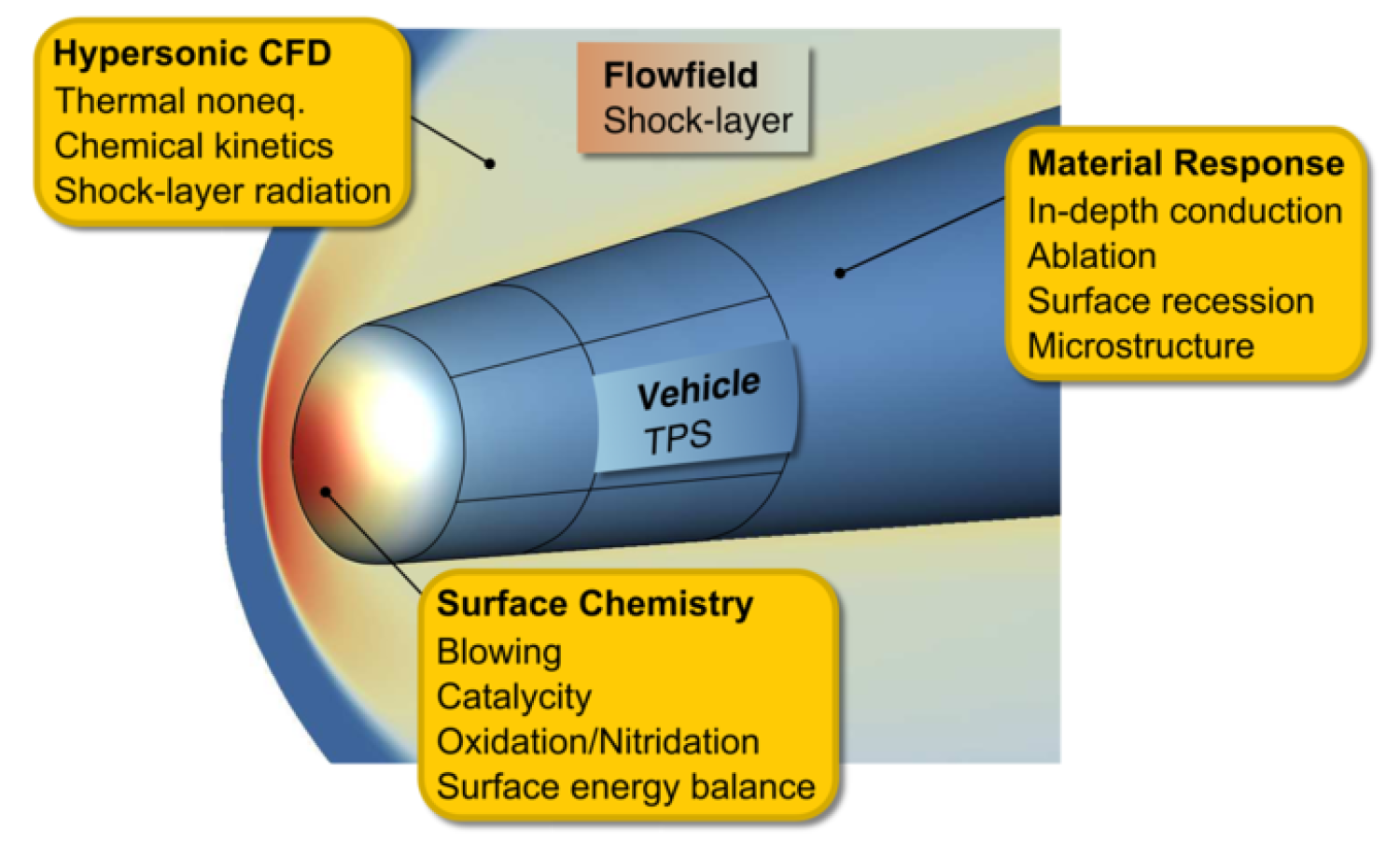
Figure 1. [1]
Building on the latest theories and modeling techniques available in the NGPDL, new material-environment interaction models are being explored which will aid the hypersonic vehicle designer and improve understanding of high temperature material capabilities. Of particular interest are various carbides, such as silicon-carbide (SiC) and di-borides, such as zirconium-diboride (ZrB2). A number of UHTC candidate materials are shown in the figure below, plotting each in terms of their melting point and the melting point of their corresponding oxidation states.
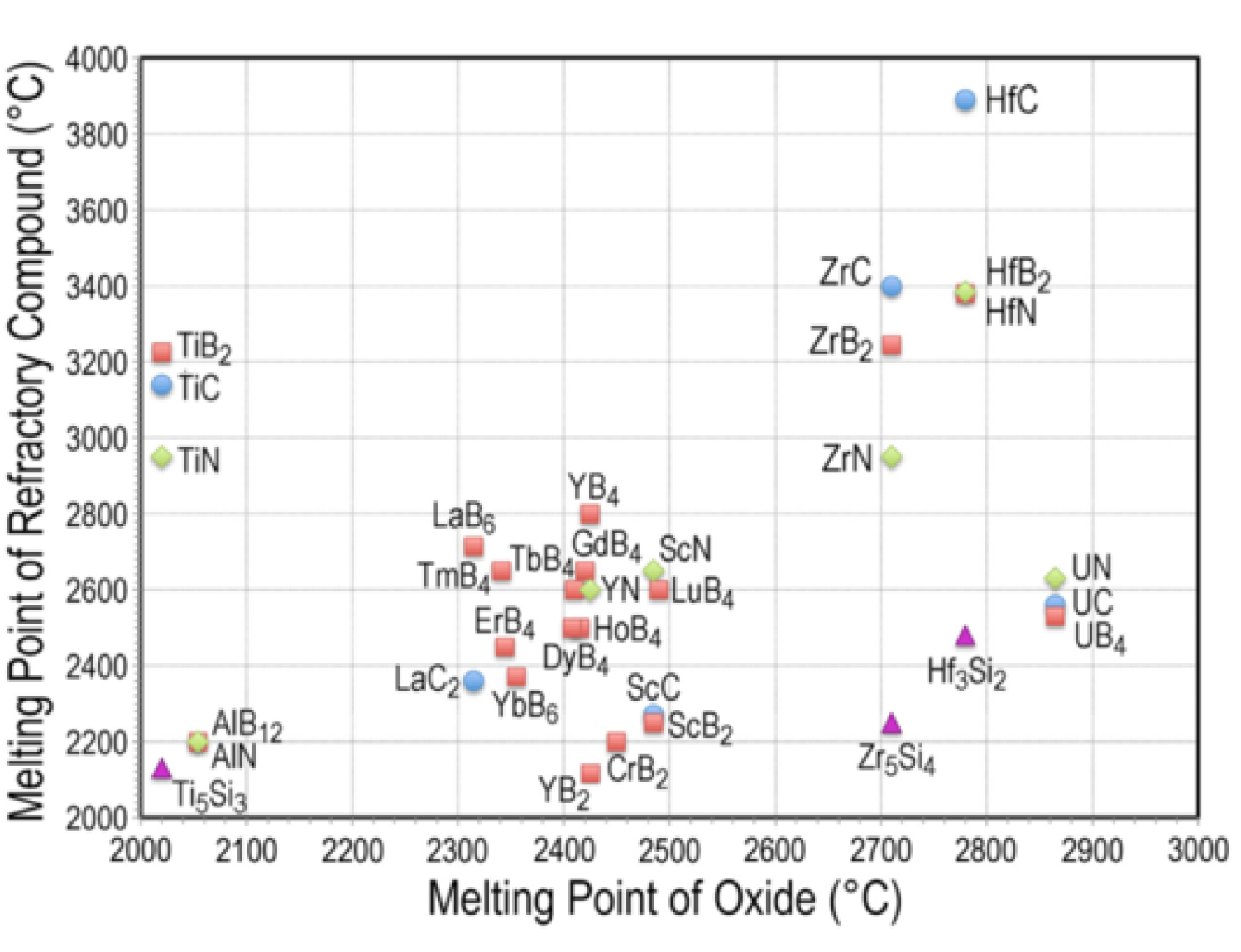
Figure 2. [2]
There are two parts to modeling material-environment interactions - the material model itself, and the Computational Fluid Dynamics (CFD) or material response framework. Material models describe the surface chemistry, morphology of the microstructure, change of phases, and any in-depth chemical processes that ultimately affect the surface chemistry, such as in the figure below. Parameters such as the oxidation rate and composition of the oxidation products are important for predicting the resulting surface heating.
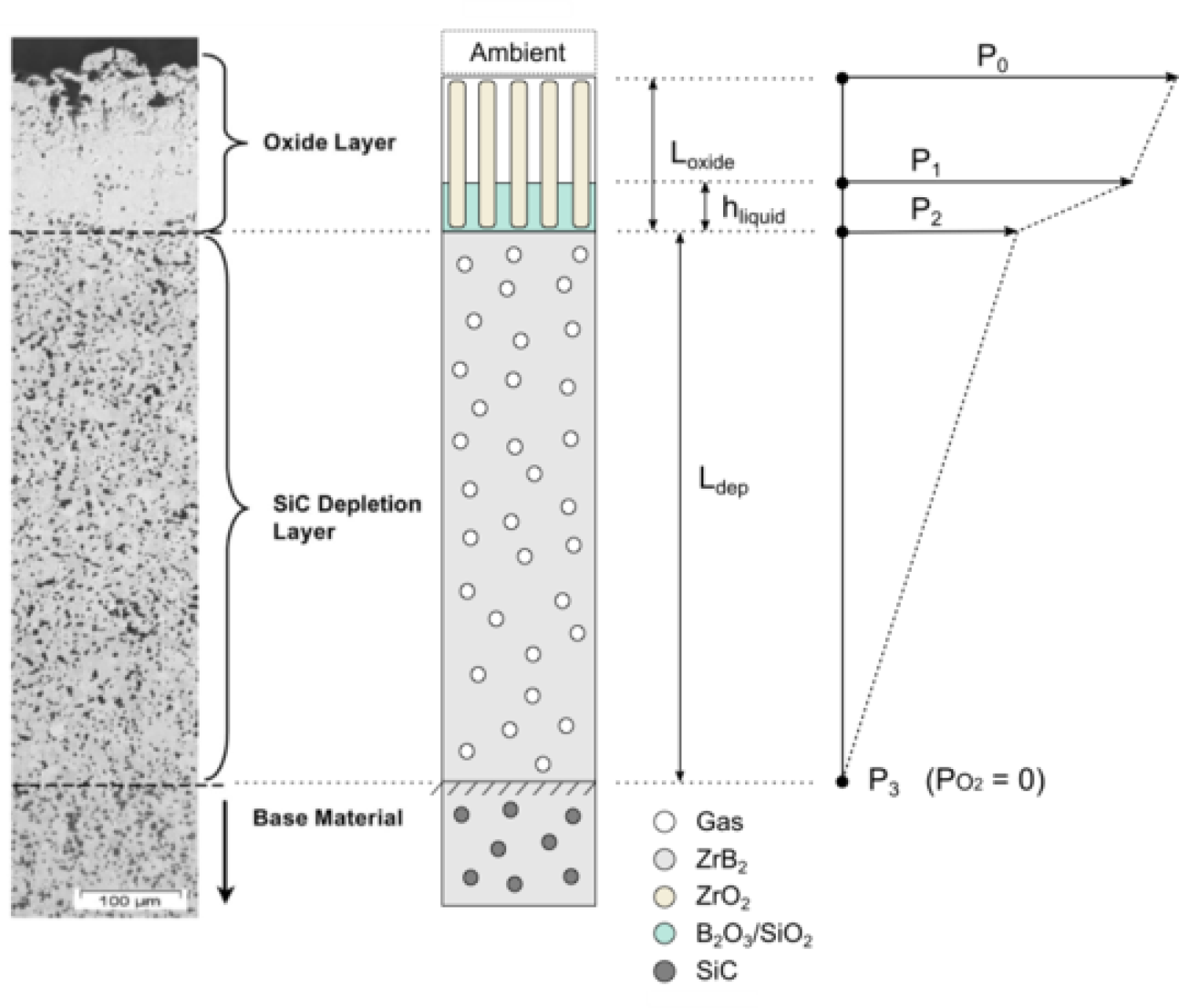
Figure 3. [2]
The underlying material-environment interaction is treated as a coupled process, involving both the material itself, and the hypersonic flowfield environment, typically modeled using high-fidelity CFD techniques. Detailed gas-surface and gas-phase chemistry are modeled in the shock layer, including any thermal and chemical nonequilibrium between the chemically reacting surface and the hypersonic environment. The figure below illustrates the predicted flowfield adjacent to the reacting surface of a SiC-coated leading edge in a hypersonic environment, showing the density of SiO, which is an oxidation product.
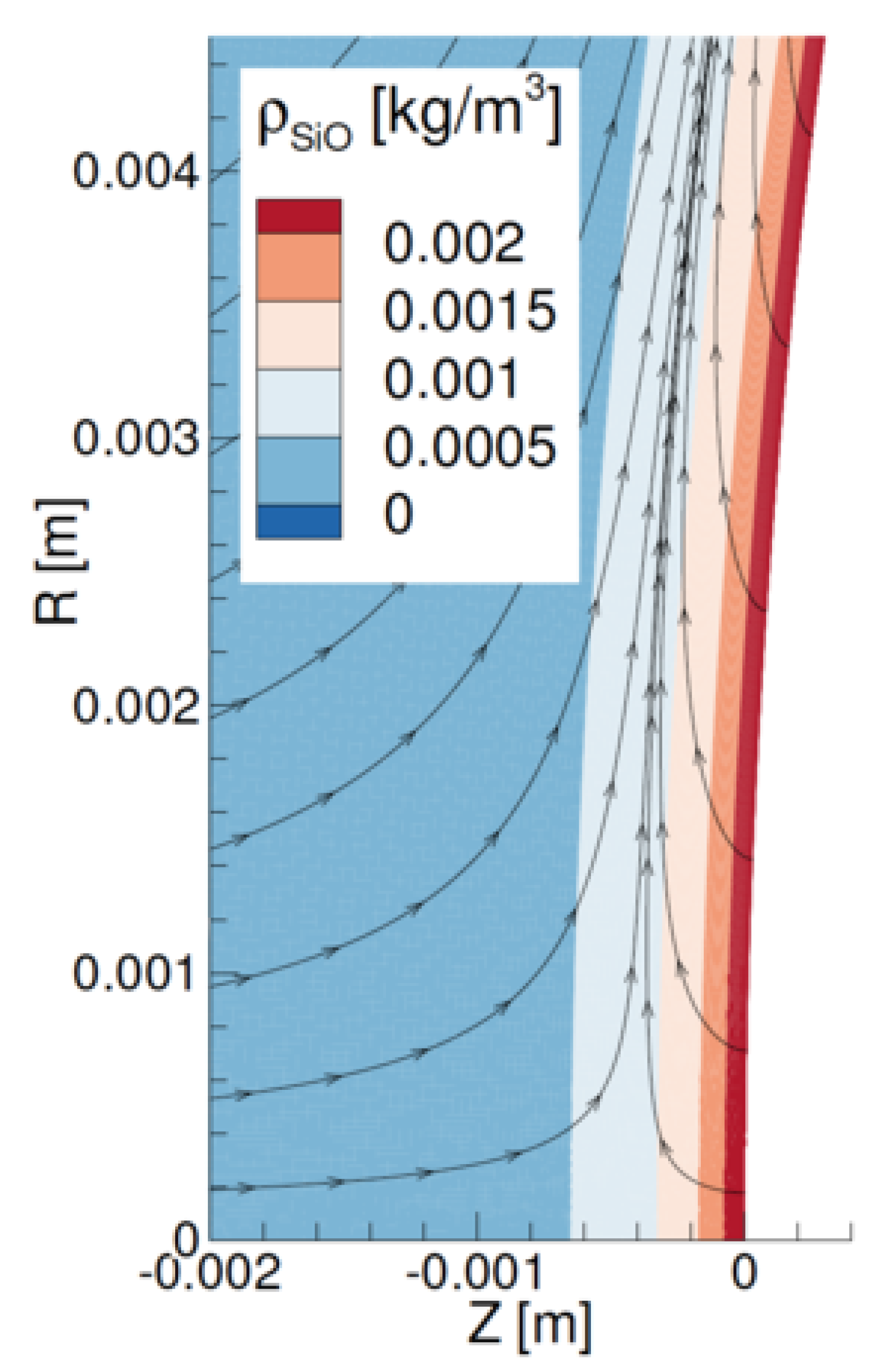
Figure 4. [2]
As new combinations of UHTC materials are developed, in-depth material response modeling is needed to reproduce and understand high temperature test results. The figure below shows a snapshot of the simulated thermal response of a HfB2 sample, after experiencing hypersonic flow conditions for 10 seconds.
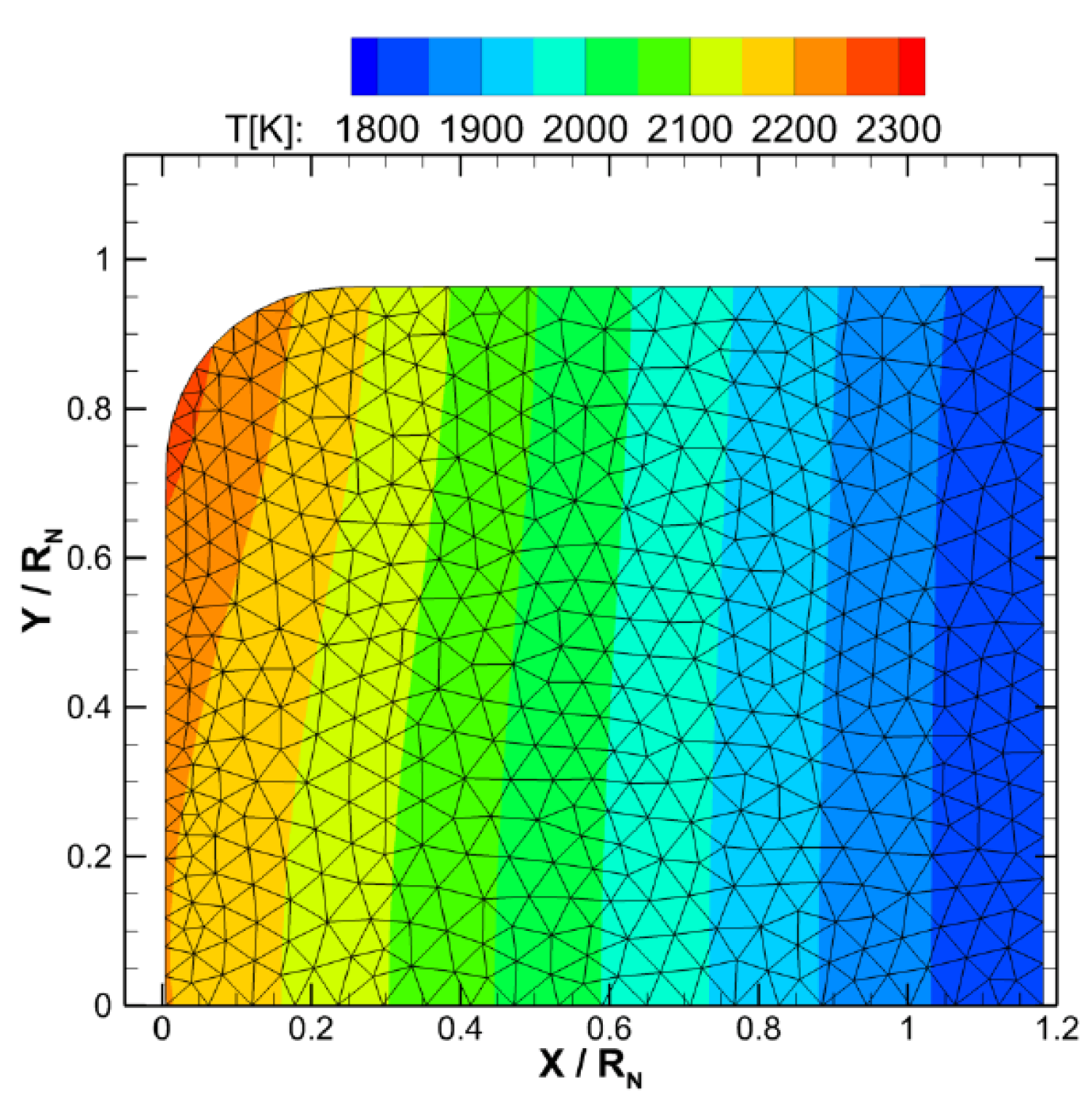
Figure 5. [3]
Investigators
Dr. Samuel Y. Chen, Dr. Daniil Andrienko, & Dr. Nicholas S. Campbell
Acknowledgments
The NGPDL gratefully acknowledges the Office of Naval Research for funding this work.
References
[1] Chen, S. Y., Modeling of Material-Environment Interactions for Hypersonic Thermal Protection Systems, Dissertation, University of Michigan, 2020
[2] Poerschke, D. L., Novak, M. D., Abdul-Jabbar, N., Kramer, S., and Levi, C. G., Selective active oxidation in hafnium boride-silicon carbide composites above 2000C, Journal of the European Ceramic Society, Vol. 36, No. 15, 2016, pp. 3697-3707.
[3] Campbell, N. S., Chen, S. Y., Boyd, I. D., Gasch, M. J., and Ellerby, D. T., Unified Material-Environment Interaction Model for Binary fUHTC Composites, AIAA paper 2021-3168. 2021.