Equipment Sharing & Efficient Space Use
17 reasons why managed, shared research equipment benefit institutions:
- Efficient purchasing: Shared equipment facilities help avoid duplicative equipment purchases and enable scientists to make better use of the resources we already have on campus.
- Space Utilization: Better space utilization minimizes the need to grow in laboratory space on campus. Lab space is very expensive space to build and maintain and typically energy intense because of ventilation needs.
- Strategic use of start-up funding: Instead of start-up dollars leaving campus when new research faculty purchase more equipment resources for their own lab that we may already have on campus, those start-up funds can stay on campus supporting existing shared equipment facilities and even expanding the equipment capabilities of those facilities.
- Time savings for researchers: Managers of shared equipment facilities save researcher time by helping them locate the equipment resources that they need and taking care of logistics that would pull them away from research (such as maintaining equipment and training new equipment users).
- Access to expertise: Managers of shared equipment facilities provide expertise to help with experimentation and trouble shooting. Skills and knowledge are transferred far more efficiently to researchers.
- Recruitment: Shared equipment can attract top scientists to campus and enable them to get started faster by providing immediate access to a wide range of resources and expertise. It takes a long time for a new faculty member to set-up a lab for research. With access to theright shared resources, getting started faster also means being able to start writing grant proposals sooner.
- Equity and Inclusivity: Managed shared equipment enables researcher access to research equipment and expertise regardless of a scientist’s, department's or institution's level of funding or support. NIH studies have found that white researchers are more likely to get research funding than black researchers.
- Energy and resource efficiency: By not duplicating equipment resources unnecessarily and using lab space more efficiently, energy and resources are utilized more efficiently on campus.
- Expanding research capabilities and grant opportunities: Shared equipment facilities provide scientists with access to equipment resources that they would otherwise not have, thus opening the door to greater research capabilities and more grant opportunities.
- External funds captured: Providing appropriate locations for external users (such as companies and collaborators) to access managed resources for a fee brings in outside dollars which furthers support of shared equipment resources and research on campus.
- Staying on the cutting edge of technology: The latest technology in research equipment can be more easily afforded when a pool of researchers are using a shared piece of equipment rather than many using each of their own. This also reduces the number of service contracts needed (and associated costs) since there are fewer pieces of equipment.
- Academics: Opportunities for classes and students to access equipment for learning experiences is simpler when equipment is in a shared facility with a manager, rather than tucked away in an individual lab. The manager can provide trainings to individual students or to an entire laboratory class.
- Compliance: Shared equipment facilities demonstrate campus compliance with Code of Federal Regulations (CFRs) that require equipment sharing and avoiding duplicate purchases where possible (2 CFR 200.313 (c)(2) and 2 CFR 200.318 (d) & (f)). Managers of shared equipment facilities can also serve as key contacts/partners for research administrators to ensure accurate equipment tracking and compliance with other federal regulations.
- Resiliency: Having critical resources co-located in shared spaces enables campus to better prepare for emergencies and better plan for building spaces that are a priority for back-up power infrastructure in case of an extended loss of electrical power.
- Rigor and reproducibility: This has become an increasingly important topic to NIH after publications demonstrated that only about 50% or less of life science research could be reproduced resulting in $28 billion/year spent in the US on research that is irreproducible. While there is great pressure to complete research and publish among scientists working in faculty labs, the pressure on managers of core facilities is to provide outstanding science and service. Thus, at the 2019 Association of Biomolecular Research Facilities (ABRF) conference, some universities presented that they are looking to cores to help their universities meet the increased scrutiny and pressure from research sponsors for scientific rigor and reproducibility.
- Safety: University research labs educate the next generation of scientists and thus can have frequent turnover of members. Managers of shared facilities often are in their positions for longer periods of time and are regularly available to provide support and oversight. As a result, they have the presence, experience, and expertise that enables them to provide consistent, quality training of users that contributes to a safe research environment.
- Responsible use of taxpayer dollars and demonstrating responsible use of funding to research sponsors: For the many cost benefit reasons given above, equipment sharing is the right thing to do because it leads to optimized use of taxpayer and research sponsor dollars.
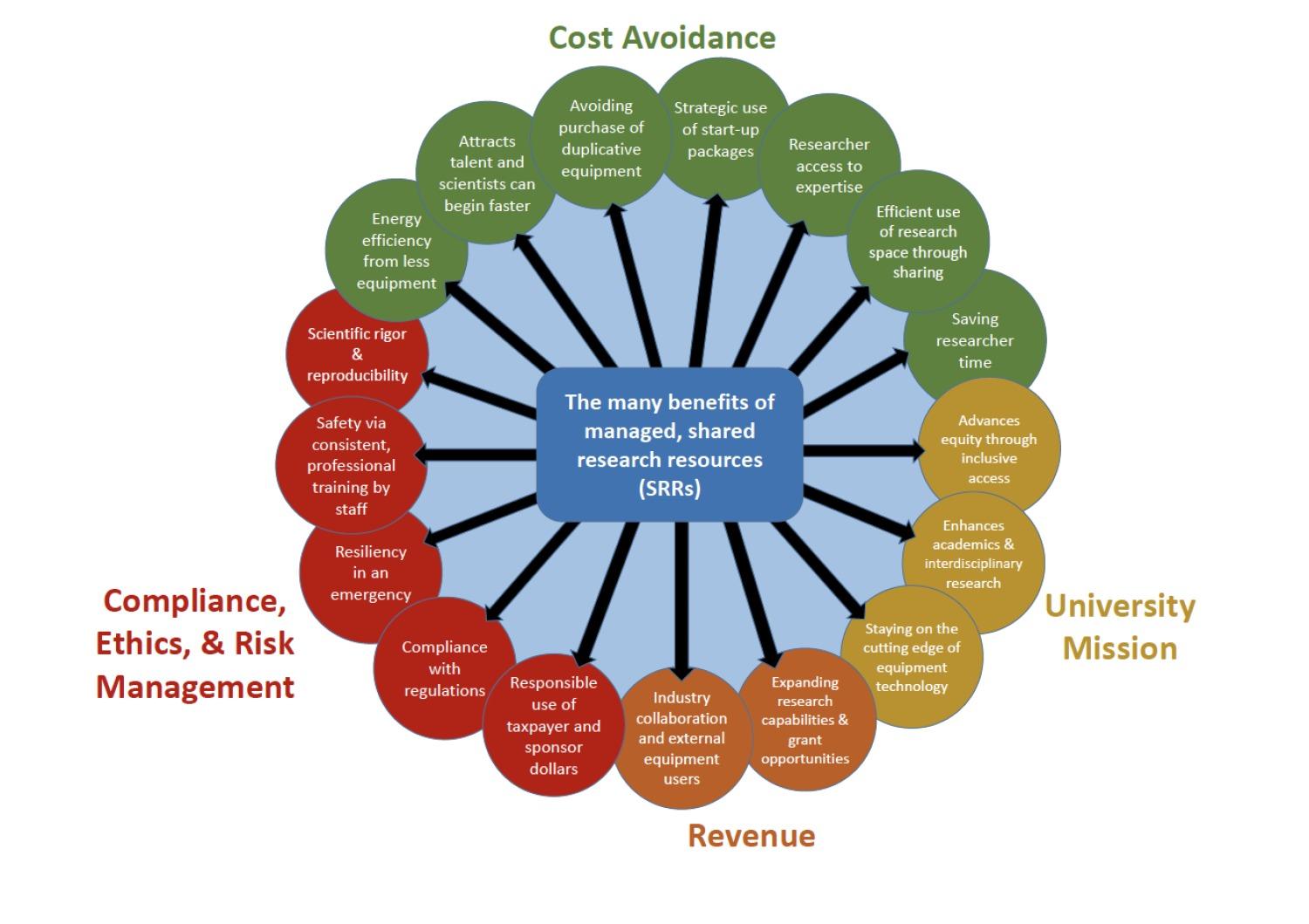
Suggestions to make shared equipment resources more efficient and to maximize impact
- NIH - Association of Biomolecular Research Facilities (ABRF) Workshop Proceedings from a 2015 "Workshop on Enhancing Efficiency of Research Core Facilities"
Challenge, Solutions, Best Practices, and more... - Maximizing Shared Research Resources - from FASEB
- FASEB created a report to summarize and aid the research community with finding funding for shared instrumentation. This resource helps benefit efficiency and the value/impact of research dollars by
- sharing best practices to maximize researcher access
- helping identify the best funding opportunity that will fit the research community needs
- providing info on obtaining second hand instrumentation
- providing information on ways to locate existing instrument resources
Code of Federal Regulations (CFRs) requiring sharing and avoiding duplication:
- Uniform Guidance Title 2 CFR 200.318 d: “The non-Federal entity's procedures must avoid acquisition of unnecessary or duplicative items. Consideration should be given to consolidating or breaking out procurements to obtain a more economical purchase. Where appropriate, an analysis will be made of lease versus purchase alternatives, and any other appropriate analysis to determine the most economical approach.”
- Uniform Guidance Title 2 CFR 200.318 f: "The non-Federal entity is encouraged to use Federal excess and surplus property in lieu of purchasing new equipment and property whenever such use is feasible and reduces project costs."
- Uniform Guidance Title 2 CFR 200.313 c2: “During the time that equipment is used on the project or program for which it was acquired, the non-Federal entity must also make equipment available for use on other projects or programs currently or previously supported by the Federal Government, provided that such use will not interfere with the work on the projects or program for which it was originally acquired. First preference for other use must be given to other programs or projects supported by Federal awarding agency that financed the equipment and second preference must be given to programs or projects under Federal awards from other Federal awarding agencies. Use for non-federally-funded programs or projects is also permissible. User fees should be considered if appropriate.”
A couple of examples of shared equipment websites:
- UC-Santa Barbara’s UC-Santa Barbara Shared Instrumentation Site
- CU-Boulder Biochemistry Shared Instrument Pool in JSCBB
- Enables sharing of more common, general-use equipment rather than just very expensive pieces of equipment
- The pool also has a gradual approach to adding equipment (for example, adding equipment as faculty retire and needs are discovered) which is a model that avoids a heavy handed approach and likely could work in other departments