400 g-ton Centrifuge
The 400 g-ton centrifuge, designed by Wyle Laboratories and fabricated by Alabama Dynamics, began operation in 1988. It has an asymmetrical rotor arm with a swinging payload platform on one end and a fixed counterweight compartment on the other. The operating radius with the swing platform extended is 18 feet (5.49 m). It can accomodate a payload volume and mass of 4x4x3 ft (1.22x1.22x0.91 m) and 4000 lb (17.8 kN) respectively.
A 900 horse-power (671 kW) Direct Current (DC) drive system powers the centrifuge through a right-angle gearbox with a 6.4 to 1 gear reduction. The centrifuge is capable of accelerating a payload to a maximum of 200g in about 14 minutes. Four large pneumatically actuated disk brakes are used to stop the centrifuge in emergency situations. Other prominent features of the centrifuge include a cooling system along the centrifuge chamber wall, an active in flight balancing system, and a dedicated real-time control and monitoring system.
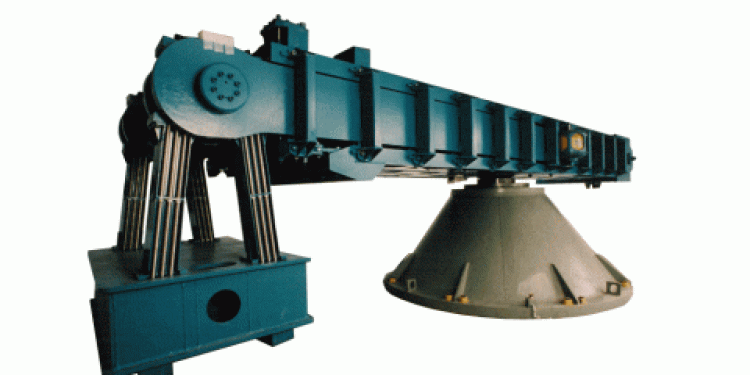
The data aquisition system for the 400 g-ton centrifuge includes a NI PXI data acquisition system combined with a 12-slot SCXI chassis, with modules suitable for signal conditioning for LVDTs, strain-gauge-type sensors, accelerometers, capacitance-type differential pressure transducers, high speed cameras. Motor control capabilities are also possible to operate brushed electric servomotors, solenoids, and electronic flow valves. Camera acquisition software can be used to track deformation of points or planes. The 400 g-ton centrifuge includes 3 hydraulic rotary union lines which can be used to supply pressurized fluid to the centrifuge platform.
SolidWorks Model
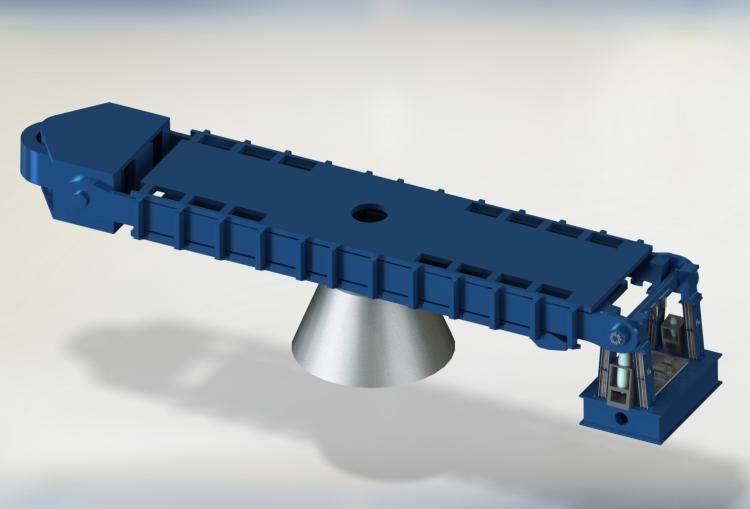
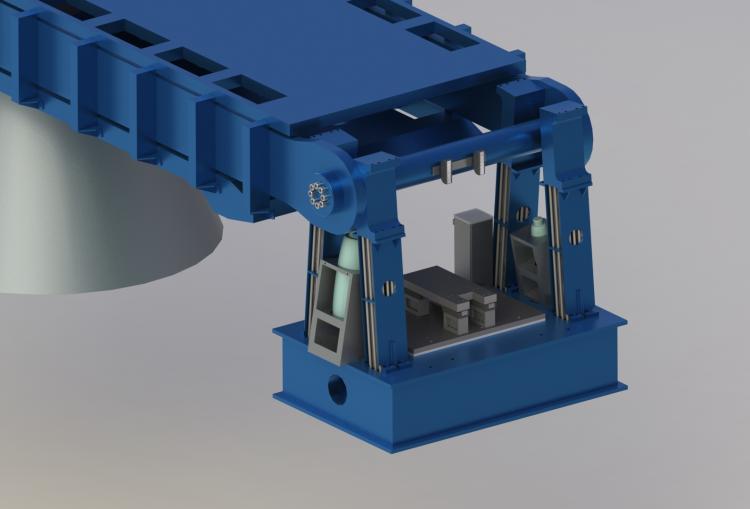
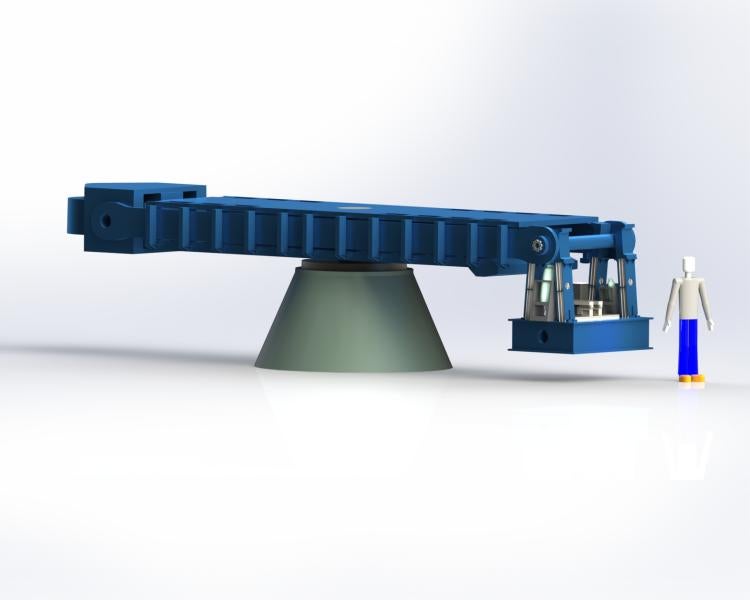