Chemical Safety

Universities are not immune to accidents involving chemicals and unfortunately some of the accidents that have occurred have been fatal. There are lessons that can be learned from these accidents that can better prepare us for working with chemicals in our labs. The following video captures 3 University accidents that involved the mismanagement of chemicals with dire consequences. This is a good learning opportunity to understand what can go wrong and what happens when the puzzle pieces are missing. Experimenting with Danger -Laboratory Safety case study
There are an estimated 30,000+ chemicals available commercially today, with more being added all the time. With this many chemicals out there, it can be challenging to keep up with all the safety information that is being generated. Likewise, new compounds and materials are being made within our labs that may also have their own unique qualities that can pose their own safety hazards.
It is important that in handling chemicals that we look at the 4 pieces of this puzzle to make sure all aspects of safety are addressed.
Procedures & Protocols

Procedures/protocols need to be reviewed and updated as new information becomes available or at least reviewed annually to make any changes.
They also need to be made available to all department members who may use the chemical. Having them available in a shared location, such as a server file, makes them easily accessible and provides a continuity in information for others to use.
It is important that anyone using a protocol first be trained on the protocol by their PI in their lab.This assures proper understanding of the protocol and allows for questions to be asked during this process.
Following the steps in the protocol requires the employee or student to participate in this process to assure their safety.
Chemical Safety Training
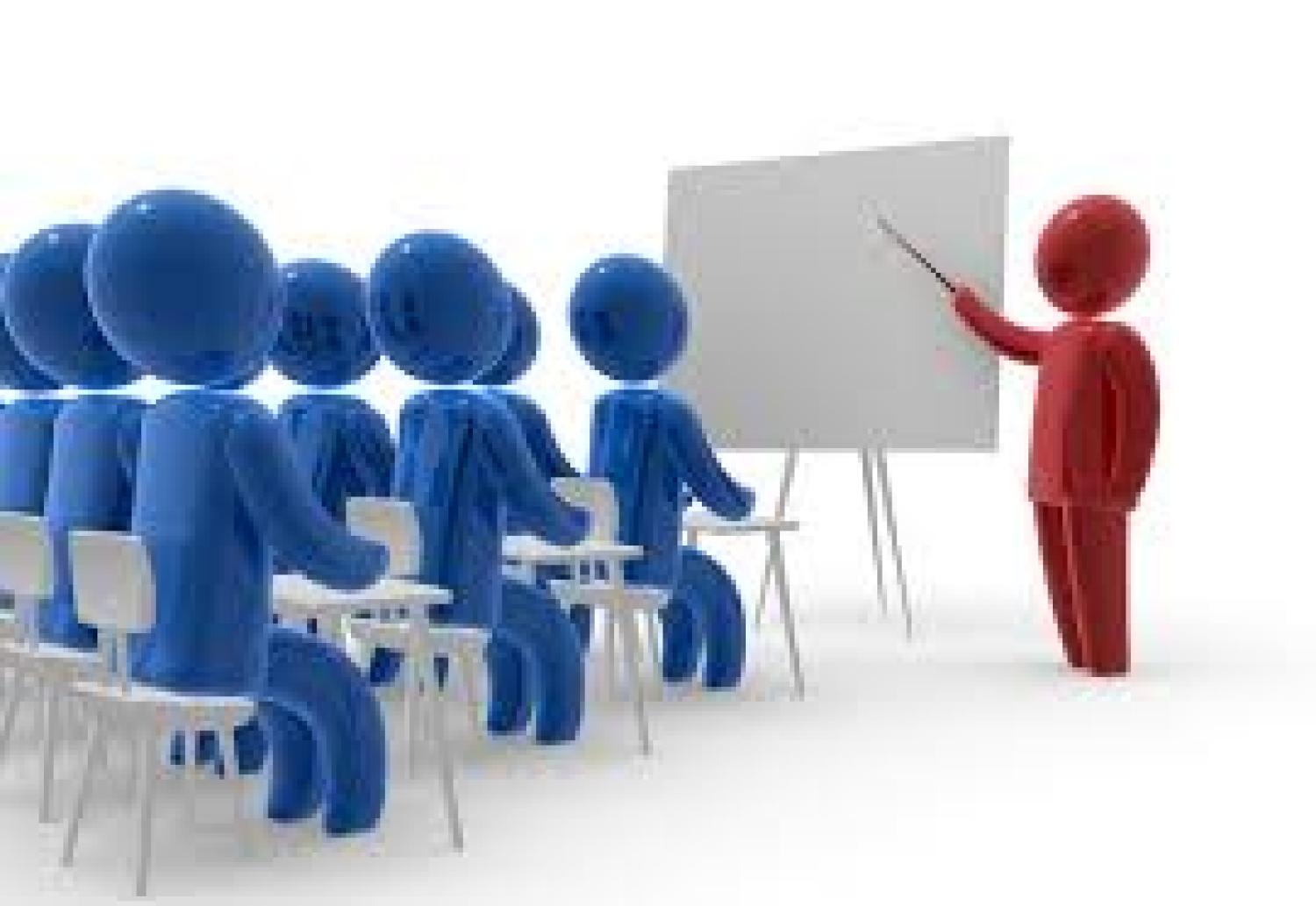
The EH&S department cover very basic concepts with chemical safety and this is a great start to build on for additional training that would cover more specific procedures with chemicals.
The best resource for chemical safety training is right in our backyard. When it comes to knowledge of chemicals, the Chemistry departmental Faculty are the experts within this field.
Each PI is responsible for training their lab members on proper chemical safety and use. If you are unclear about how to properly use a chemical, consult with your PI.
Don't miss an opportunity to keep learning, stay engaged and participate in training programs.
Hazard Communication
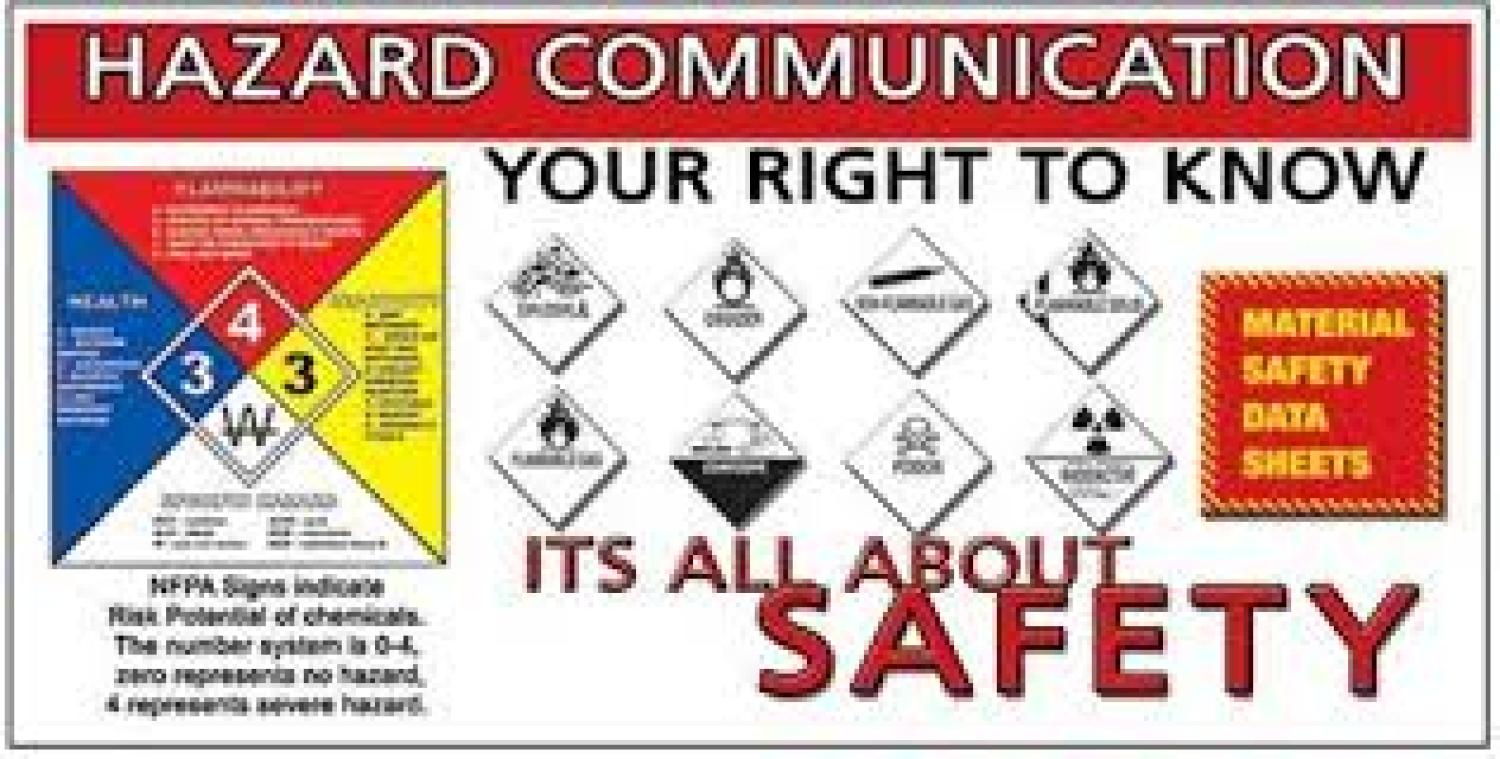
Chemical Manufacturers are required by law to develop a MSDS (Material Safety Data Sheet) for every chemical that is made. The international community has pushed to standardize the format of the MSDS' so that there is continuity among manufacturers. There are 16 distinct catagories that contain all the known information for the chemical. Those 16 items are as follows:
- SECTION 1: Identification of the substance/mixture and of the company/undertaking
- 1.1. Product identifier
- 1.2. Relevant identified uses of the substance or mixture and uses advised against
- 1.3. Details of the supplier of the safety data sheet
- 1.4. Emergency telephone number
- SECTION 2: Hazards identification
- 2.1. Classification of the substance or mixture
- 2.2. Label elements
- 2.3. Other hazards
- SECTION 3: Composition/information on ingredients
- 3.1. Substances
- 3.2. Mixtures
- SECTION 4: First aid measures
- 4.1. Description of first aid measures
- 4.2. Most important symptoms and effects, both acute and delayed
- 4.3. Indication of any immediate medical attention and special treatment needed
- SECTION 5: Firefighting measures
- 5.1. Extinguishing media
- 5.2. Special hazards arising from the substance or mixture
- 5.3. Advice for firefighters
- SECTION 6: Accidental release measures
- 6.1. Personal precautions, protective equipment and emergency procedures
- 6.2. Environmental precautions
- 6.3. Methods and material for containment and cleaning up
- 6.4. Reference to other sections
- SECTION 7: Handling and storage
- 7.1. Precautions for safe handling
- 7.2. Conditions for safe storage, including any incompatibilities
- 7.3. Specific end use(s)
- SECTION 8: Exposure controls/personal protection
- 8.1. Control parameters
- 8.2. Exposure controls
- SECTION 9: Physical and chemical properties
- 9.1. Information on basic physical and chemical properties
- 9.2. Other information
- SECTION 10: Stability and reactivity
- 10.1. Reactivity
- 10.2. Chemical stability
- 10.3. Possibility of hazardous reactions
- 10.4. Conditions to avoid
- 10.5. Incompatible materials
- 10.6. Hazardous decomposition products
- SECTION 11: Toxicological information
- 11.1. Information on toxicological effects
- SECTION 12: Ecological information
- 12.1. Toxicity
- 12.2. Persistence and degradability
- 12.3. Bioaccumulative potential
- 12.4. Mobility in soil
- 12.5. Results of PBT and vPvB assessment
- 12.6. Other adverse effects
- SECTION 13: Disposal considerations
- 13.1. Waste treatment methods
- SECTION 14: Transport information
- 14.1. UN number
- 14.2. UN proper shipping name
- 14.3. Transport hazard class(es)
- 14.4. Packing group
- 14.5. Environmental hazards
- 14.6. Special precautions for user
- 14.7. Transport in bulk according to Annex II of MARPOL73/78 and the IBC Code
- SECTION 15: Regulatory information
- 15.1. Safety, health and environmental regulations/legislation specific for the substance or mixture
- 15.2. Chemical safety assessment
- SECTION 16: Other information
MSDS are a great resource to use to understand the chemical that you will be working with and allow you to proactively prepare on how to use the chemical appropriately. MSDS can be found on line on manufacturers websites. In addition, a hard copy must accompany the shipment of the chemical and upon receipt the lab user needs to add it to the lab's MSDS binder. Outdated MSDS must be replaced with newer versions to assure the most current information is available.
MSDS' are not the only means to gather information about a chemical that will be used. here are other Federal agencies that also accumulate extensive data on chemicals. Some of these agencies, include NIOSH, OSHA and PubChem. In addition, throughout the safety professional communities, there are other organizations that have additional informational and resources that can be located. The campus EH&S Department is also available to answer any questions and provide guidance as well.
Chemical Inventory

In addition, Federal agencies, such as the EPA, DHS (Department of Homeland Security) require that Universities have an accurate means to account for the chemicals on their campuses. Not knowing what is onsite can create opportunities for environmental hazards and potential security threats to the campus as a whole. Taking a proactive approach to chemical inventory management and oversight is critical to assure compliance.
In order to assist department labs with complying with campus rules for chemical inventory tracking, a barcoding system and database has been administered in the MyLab module for every lab.
Chemicals must be ordered through the Purchase request system, which generates an authentic barcode for each chemical when ordered. New chemicals received through the Chemstores receiving area, are affixed with the assigned barcode and assigned to the lab that ordered the chemical.
Lab members that receive chemicals are responsible for updating the Mylab inventory information so that the correct information is current on the database. Likewise, a system must be in place for removing the chemicals off the database when discarded. Chemical inventories must be audited annually to keep the database up to date. Assistance with this process can be provided by the department.